$1.8 Million Savings on an RCC Catalyst Line
- IMS team
- May 29
- 2 min read
This article presents a case in which a Houston-based refinery used a Digital Twin and a Zero-Defect work process to replace worn out sections of a 60-inch RCC catalyst line. The Digital Twin was created by digitizing the project scope with a 3D laser scanner. Data network uncertainty was closely controlled with proprietary algorithms to achieve the engineering tolerances required.

Project Summary:
The worn out section of duct needed to be replaced while reusing the remainder of the duct, including its existing flanged connections. Complex 3D cuts had to be made to remove the worn sections. Critical large bore tie in points to existing-to-remain flanges required that the new duct fit to very tight tolerances. To maintain schedule, the owner’s goal was to complete the reassembly with a single crane lift with no test fitting. The ductwork contained a series of beveled sections, complicating an already difficult geometric configuration. A typical leave-long-and-trim solution was not feasible given the geometry. A change in length at one tie point would change the angle and elevation of other tie points further down the line. $1.5 million in direct savings were reported by owner ROI estimated at 3,100%
Work Process:
The laser scanner was used in conjunction with 3D CAD software to create an as-built model of the duct, which was then modified for design changes required in the replacement.

The design model was projected into the Digital Twin and checked for fit and function by owner representatives.

Each duct section was digitized at the fabrication yard to ensure dimensional accuracy.
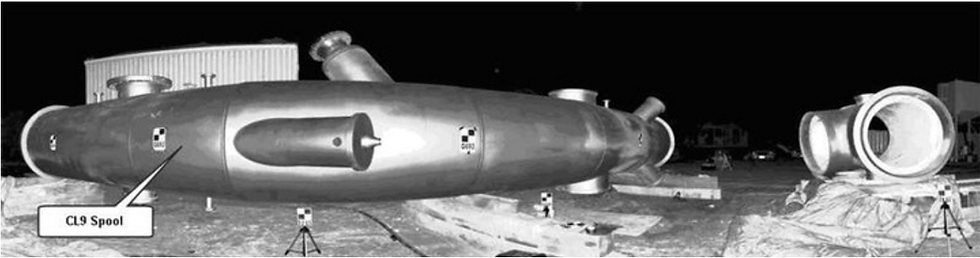

Comentarios